An aggregates company recently found out that its hot works procedures and contractual provisions weren’t exactly “fire proof.” What caused it to lose its GB pound 4 million claim against the welding firm that started the blaze?
The sequence of events
On Sunday, February 3, 2008, staff of G M Welding & Engineering (GM) carried out repair works at a plant owned by United Marine Aggregates (UMA) in Greenwich. The work took place in an area known as the “top box,” which was part of the aggregate grading system. It was a relatively regular type of repair, so GM’s welders were very familiar with the work to be done and the methods to be used.
Critically, the underpan of the top box had a combustible rubber lining secured in place with mastic. This created a difficulty as it was unavoidable that the removal of bolts with an oxy-propane torch would produce spatter — molten metal at 1500 degrees Celsius. This was countered by water dousing, but despite best efforts, a droplet of the spatter apparently missed the water spray, burned through the mastic seal, melted through the underpan lining, and started a smouldering fire.
It was later deduced that the fire must have begun between 8:00 a.m. and 8:15 a.m., but there were apparently no signs of it, either visually or by smell, within the first hour or so, when the welders were still in the area.
At 9:50 a.m., smoke was observed to be pouring from the building, and the fire, now in full force, caused extensive damage to the plant before it could be extinguished.
What precautions were demanded?
UMA had a hot works procedure adherence, which was a contractual requirement. It required the removal of sources of fuel within a 10-meter radius, and where this was not possible, such as where rubber chute linings were present, the materials were to be protected with fire blankets, etc., and damped down where possible. Other critical points examined in the later court cases were the need for a “constant check of the area to be made for any signs of fire” and for fire monitoring on completion. The period of time for monitoring was not defined, and instead it was stated, “The period of time will vary according to circumstances and the degree of risk involved (30 minutes to four hours or longer).”
Following agreement with senior management as to the method of work, the contractors hosed down the work area before and after, and also made sure that a continuous jet of high pressure water was directed onto the side of the underpan while the hot work was being carried out. Fire resistant pads were not used because these were regarded as impractical in the circumstances.
In court
After an eight-day trial at the High Court, Queen’s Bench Division, Technology and Construction Court, it was determined that the welding company G M was not liable. But UMA appealed — giving rise to the case United Marine Aggregates Ltd v. G M Welding & Engineering Ltd & Ors & Novae Syndicates Ltd [2013].
The appeal court, however, agreed with the judge at the original hearing that the work had been carried out diligently and it was not reasonably foreseeable that a fire of the type that occurred would start so deeply within the lining and therefore be undetectable by smell for more than an hour. The appeal was dismissed.
Learning points?
The case shows that when hot work is introduced into a high-risk area, the risk assessment and procedures need to be made site specific. For example, the looseness with which the designated fire watch period was defined did not help UMA’s case. It was also determined that the term “constant fire watch,” as required by the hot works procedure, did not necessarily mean that an individual needed to be solely dedicated to the task.
A specific assessment might also, at least with hindsight, draw out particular risks from hidden combustible linings in adjacent parts of plant/buildings. And had the actual procedure to be followed been spelled out and issued with a hot work permit, UMA might possibly have found itself in a stronger position.
Another factor for clients to consider is how they go about agreeing upon procedures. In this case, it was deemed that the Hot Works Procedure document had been effectively overridden when UMA senior management agreed upon a slightly different system of work, one not entailing the use of fire-resistant matting.
2023 Fire Safety eBook – Grab your free copy!
Download the Fire Safety in 2023 eBook, keeping you up to date with the biggest news and prosecution stories from around the industry. Chapters include important updates such as the Fire Safety (England) Regulations 2022 and an overview of the new British Standard for the digital management of fire safety information.
Plus, we explore the growing risks of lithium-ion battery fires and hear from experts in disability evacuation and social housing.
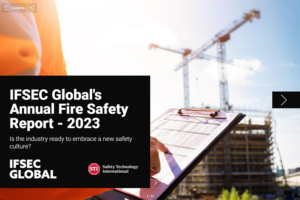