Two suppliers of factory machinery have been found 80 percent liable for a fire that destroyed about a third of a bakery factory.
In a recent case heard in the Scottish Court of Session, an insurer sought to recoup some of its costs for a GB pound 6,788,566 fire payout. The details of the case contain some useful learning points for those who are assessing fire risk in manufacturing plants.
The fire
The fire broke out at a Bathgate factory owned by United Central Bakeries Ltd (UCB) on 1st November 2006. It started in an area where naan bread was made. The seat of the fire was in a helical conveyor system known as a heliveyor.
The court assessed the fire was probably caused when burning pieces of naan exiting the oven became lodged between plastic modules of the heliveyor belt. The prolonged contact with hot or burning bread would have caused the belt to melt and ignite. Drops of melted materials then landed on lower levels, spreading the fire rapidly.
Why did the belt catch fire?
Essentially, with hindsight, the belt material was not suitable for the application. The belt was made of Polyacetal-POM, a type of thermoplastic commonly used in bakeries. On the face of it, it appeared right for the job.
The problem is that cooking flat breads involves much higher temperatures than other breads. The naan was sprayed with oil and then baked in an oven at 400˚C. Sometimes if the bread stuck to the base of the travelling oven, it would go around twice and then come out of the oven in fragments which would be alight. The maximum tolerance of the belt was around 164˚C, and the manufacturer’s brochure recommended a maximum of 90˚C for product carried.
Knowing all this, it’s evident that burning pieces of bread might cause a fire. Unfortunately, it seems that no single person had all these facts.
Forbo Siegling and Spooner Industries
Despite the mistake, the judge concluded that the machine’s manufacturer, Spooner Industries Ltd., and the belt’s manufacturer, Forbo Siegling (UK) Ltd., were not to blame for the design of the equipment. There was no breach of the Sale of Goods Act 1979, the judge ruled, because POM belting was widely used in bakeries, and the client had not alerted them that burning product regularly found its way on to the conveyor.
However, both of these parties, along with the client, had missed a chance to correct the defect when a fire broke out in 2003. After that fire, both manufacturers sent representatives to the site to try to identify the cause. UCB managers were concerned that the belt material would sustain a flame, whereas similar looking materials nearby on the production line did not.
In subsequent emails, both Siegling and Spooner gave reassurances that the belt was made of suitable materials, and that it was very unlikely that burning naan would set fire to it. Along with the reassurances, they provided a data sheet that had been requested by the client.
Apportionment
The mistake made by the client was not reading the data sheet. One manager said this was because it was “technical” — he perceived it would be too difficult to interpret. As a result of this error of judgment, Lord Hodge found UCB to be 20 percent liable. He said in the ruling:
UCB’s senior managers asked for the data sheet but did not consider it properly when they received it. UCB had the best knowledge of the temperature of ovens. It had the most direct opportunity of testing the temperature of the naan breads exiting oven and of observing the frequency of burning naan breads reaching the heliveyor.
Spooner and Siegling were apportioned more of the blame — 40 percent each.
As the supplier of the heliveyor Spooner was guilty of both negligent misstatement and negligent failure to warn…
Spooner and Siegling should have emphasised the advice about temperatures and flammability in the data sheet and also Siegling’s recommendation in its brochure that the product should not cause the belting to exceed 90˚C. Further, as they were unaware of the temperatures of the customer’s product but were aware of its concerns of the effect of burning naan breads, they should have advised UCB to investigate, or assisted in investigating, the effect of burning naan breads on the POM belting.
In this case, the client should have stuck to its guns. It had been on the right track when it carried out basic tests and expressed its doubts. However, it didn’t follow up on evidence of the belt being scorched in the three years between the two fires. The case teaches us to be wary of opinions on safety-critical matters given by interested parties, and to trust our instincts.
It also underlines the value of ensuring enough time is invested up front in the design of bespoke equipment. Had the designer been more aware of the temperatures and the way in which the process operated, the designer likely would have taken better account of the burning pieces of bread being emitted.
2023 Fire Safety eBook – Grab your free copy!
Download the Fire Safety in 2023 eBook, keeping you up to date with the biggest news and prosecution stories from around the industry. Chapters include important updates such as the Fire Safety (England) Regulations 2022 and an overview of the new British Standard for the digital management of fire safety information.
Plus, we explore the growing risks of lithium-ion battery fires and hear from experts in disability evacuation and social housing.
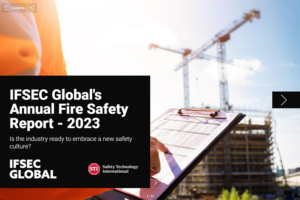