The company held responsible for a devastating factory explosion has failed in its bid to pass on some of the liability to its liquefied petroleum gas supplier. What action should companies take if they have underground LPG pipework?
The explosion
On May 11, 2004, a massive explosion ripped through the ICL Plastics factory in Glasgow. Nine people were killed, and many more were injured in the collapse of the four-story building. On investigation, it was determined that the blast was caused by LPG that had leaked from an underground metal pipe into the factory’s basement.
The pipe had been installed in the 60s and had been inadequately protected. It was ungalvanized, had no protective covering, and had been backfilled with unsuitable material including a large concrete slab. There was also no sleeve sealing around the pipe where it entered the building. The pipe had corroded over time and developed a large crack. The leaking LPG ran along the line of the pipe and into the basement of the factory.
The prosecution
In August 2007, ICL Plastics Ltd. and ICL Tech Ltd. pleaded guilty to contravening the Health and Safety at Work Act 1974 and were each fined GB pound 200,000. Specifically, the charges they pled guilty to were that there had been failures:
- To make a suitable and sufficient assessment of the risks to the health and safety of employees while at work in failing to identify that the pipework conveying LPG from the bulk vessel storage to the premises presented a potential hazard and risk
- To appoint one or more competent persons to assist in carrying out such risk assessments
- To have a proper system of inspection and maintenance in respect to the LPG pipework concerned
- To ensure, so far as was reasonably practicable, that the pipework was maintained in a condition that was safe and without risk to employees
HSE inspectors had asked for part of the pipework to be excavated for inspection in 1988, but the request was not acted upon, nor enforced. ICL Plastics explained in its defense that on receipt of a letter from the HSE requiring various actions to improve its LPG installation, it had sought advice from its supplier, Calor. The supplier had suggested that rather than excavate a section of the pipework to determine its condition, it could carry out a pressure test and an inspection of visible parts of the pipe. A letter from the HSE apparently accepted the proposal.
The inquiry and beyond
In 2009 there was a public inquiry under the direction of Lord Gill. The subsequent report identified serious weaknesses in the regime for LPG gas safety.
Following the prosecution and inquiry there have been multiple claims for compensation. In a recent case ICL Tech, ICL Plastics, and Stockline Plastics Ltd. sought a contribution from Johnston Oils Ltd. (JO) towards these compensation costs on the basis that JO would have been found liable in damages to the injured parties if they had sued it.
JO had installed a new supply tank in 1998 shortly after it took over the contract to supply LPG to the site. It had carried out leak detection and pressure testing at the time, but had not carried out any further inspections as it was the customers’ responsibility to ensure the safety of its own pipework.
The court found that JO had acted reasonably. It was not under any duty “to inquire about the condition of the customer’s pipework and to give unsolicited advice to the customer to investigate and maintain it.”
Responsibilities
It’s clear that organizations that use LPG can’t expect to pass on responsibility for their installation to their suppliers. It’s been found that many of the estimated 40,000 commercial users of LPG don’t understand their responsibilities. In reality they are normally responsible for all of the pipework except for the tank and any pipework leading to the first regulator.
Following the criticism of the Inquiry, the HSE began a survey and inspection programme alongside the UKLPG (the trade association for the LPG industry). As a result, 33,000 surveys have been returned, and risk ratings have been undertaken. Those with buried metallic LPG pipes falling within the “higher risk” category have been asked to replace them with polyethylene by the end of this year. The remainder will need to be replaced by 2015 — though there’s talk that the deadline may be extended due a shortage of capacity within the industry to do the work.
HSE makes it clear that the preferred strategy is for pipework replacement, though an alternative is that duty holders “implement a robust inspection, examination, and maintenance strategy to ensure pipework continuing integrity.”
Want to know more? The HSE has issued a “topic inspection pack” used by its inspectors. Details of the high-level plan for pipework replacement have also been published.
2023 Fire Safety eBook – Grab your free copy!
Download the Fire Safety in 2023 eBook, keeping you up to date with the biggest news and prosecution stories from around the industry. Chapters include important updates such as the Fire Safety (England) Regulations 2022 and an overview of the new British Standard for the digital management of fire safety information.
Plus, we explore the growing risks of lithium-ion battery fires and hear from experts in disability evacuation and social housing.
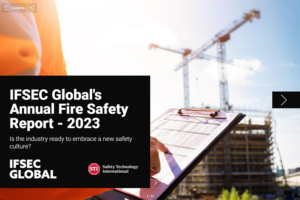